Stained Glass Window Restoration
Windfall Light Stained Glass
Sam Lopp has become a respected stained glass artisan through his many years of honing his craft. He also began teaching the fundamentals of stained glass to others. He recalls, “Through the years, I have instructed a minimum of 500 students.” During a typical six-week course, Lopp teaches the copper foil method and lead cane method. (The JHN properties utilized the lead cane method.) He says, “Putting a stained glass window together is tedious work. Frankly, only about 10% of all my students go on to do another project.”
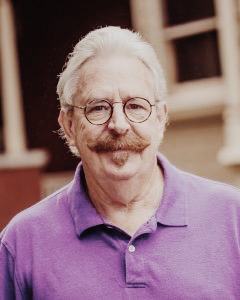
For a full window restoration like that of the JHN properties, Lopp says the first step in the process is to observe and evaluate the condition of each window (Is it sagging? Is it missing glass? Are there cracks in the lead?). The next step is to remove the windows from the sashes to get an even closer inspection of each element. He says, “What I’m finding on the [JHN windows] is that they are structurally sound, but in many cases the stained glass is coming away from the border and everything is loose from the rot of wooden sashes.” He says this is from a natural progression of deterioration due to age, sunshine, fading, heating/cooling, and gravity. Small samples of glass pieces were sent off to D&L Art Glass Supplies in Denver, Colorado to try to match the original glass as closely as possible. He says, “Only a very well-trained eye—like these experts—will notice a slight shade difference.” Each replacement piece will then be painstakingly placed back into the original window design.
Lopp says the JHN stained glass windows were facing a critical period. “Without preservation, the windows would be lost. So I’m excited to restore and rebuild them to their former glory,” he says. “This type of project is extremely unique. It is a once-in-a-lifetime project for me.”